3D Printing Phoenix is an efficient manufacturing technique for creating products. It eliminates numerous operations and set ups, reduces energy consumption, and avoids the cost of warehouse storage and transportation.
Engineers can rapidly produce prototypes to test and evaluate new designs. They can also save Engineering time by reducing the number of components required to manufacture a final part and by creating lightweight geometric objects.
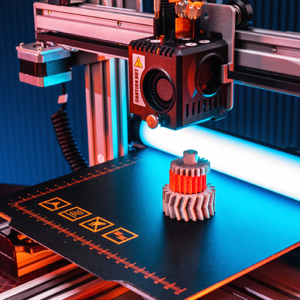
The prototyping process converts a digital design into a physical model. This step is vital in the product development cycle, allowing companies to test out a concept or feature early on and determine whether it adds value for users. This helps to eliminate unnecessary iterations and saves both time and resources.
To create a prototype, designers must first create a digital 3D model using CAD software. Then, the model is sent to a 3D printer, which creates the physical model by depositing layers of material until the object is complete. There are various types of 3D printers available, each with its own strengths and weaknesses. For example, some printers use plastic materials that are melted and deposited layer by layer, while others use lasers to fuse metal powders into solid parts.
Prototypes can be low-fidelity, which is best for exploring and validating concepts and ideas, or high-fidelity, which provides a more accurate representation of the final product. The amount of time and effort that goes into creating a prototype depends on the project’s requirements and the stage in the design process.
Once a prototype is complete, it can be tested with real users to see how well it meets the user’s needs. Feedback is collected and used to make any necessary adjustments before the final product is developed.
During the prototyping phase, it is important to establish a clear test goal. For example, if you are testing a new product interface, it is crucial to know what information the user will be able to access and how they will interact with the prototype. This will help you to target the right users for your study, which will ensure that you get a more reliable and in-depth response from participants.
Another exciting development in rapid prototyping is biological printing, which is a developing area of biomedical engineering that involves the creation of living tissue. Researchers are experimenting with ways to print living cells and scaffolding structures that support them, which could eventually lead to the creation of fully functional human organs.
Rapid Manufacturing
A number of companies are taking advantage of rapid manufacturing and its benefits. The ability to go from a computer-aided design (CAD) drawing to a physical prototype can significantly reduce the time to get products to market. Companies can also produce multiple prototypes quickly to test different aspects of a design and determine which features will work best. This is an important step in any product development cycle and allows for the most accurate and realistic testing.
3D printing is a type of additive manufacturing process that builds parts out of plastic or metal one layer at a time. It can also build multiple dissimilar pieces at once, making it ideal for complex designs. It is less expensive than other types of prototyping and production processes. The technology has been around for over 15 years and is continuing to evolve. Initially, it was very expensive but as patents expired the price of the machines fell dramatically, opening up this type of technology to more businesses.
The most common type of 3D printer uses a spool of thermoplastic filament that is melted into a liquid state by the machine’s nozzle barrel before being laid down layer-by-layer according to a program. This is the same process that occurs when you use a desktop 3D printer to print a model or gift for someone. It is an inexpensive and easy-to-use type of printing that can be used for a wide range of purposes.
Other types of additive manufacturing use different materials. The most precise method is known as material jetting, which can produce full-colour parts in a variety of materials. This is an expensive process that creates extremely detailed parts, but it can be difficult to control. This technique is most often used to make tooling or medical devices.
Traditional methods still hold a place in manufacturing, but many are turning to rapid manufacturing as a way to perform small-run productions. For example, car and aircraft manufacturers are using 3D printing to transform unibody and fuselage design and powertrain production. General Electric has even used 3D printing to produce a helicopter engine with 16 parts instead of 900, which is an enormous savings in both time and money.
Additive Manufacturing
The 3D printing process transforms virtual digital models into physical objects through layer-by-layer fabrication. This is often called additive manufacturing (AM).
This technology bridges the gap between design and production by allowing designers to make modifications in a short time.
For example, during the coronavirus pandemic, manufacturers made respirators and swabs that were quickly printed by the thousands. These are just one of many applications of this incredible technology.
Additive manufacturing is becoming the next industrial revolution, and those who embrace it will be well-positioned for success. However, it’s important to understand the basics of this technology so you can effectively harness its power.
New additive technologies are constantly appearing and developing. The plethora of options can be overwhelming and challenging to keep up with. But keeping up is critical, because the pace of innovation is relentless.
These technologies can print in a wide range of materials, from polymers to metals and ceramics. The choice of material depends on the performance and aesthetics you need for your part. For example, you might choose a polymer for a strong, lightweight part or a biomaterial for a medical device.
Some additive technologies are better suited for prototyping, while others are better for production. For example, fused deposition modeling (FDM) is ideal for making quick prototypes. It uses heat and plastic-like polymers to build layers until the part is complete. However, these parts may be brittle and require post-processing to remove support structures. Additionally, the polymer color may fade or lose its mechanical properties with exposure to UV rays.
Other AM processes are better suited for production, such as laser cured resin and stereolithography. These technologies can produce parts with a high level of dimensional accuracy and smooth surface finish. They are also capable of producing parts with complex internal architecture and can be made from a variety of materials, including metals.
3D printing has already revolutionized the aerospace industry with components that merge form and function. From the tactile surfaces of seat backs to the functional elegance of air ducts, aircraft cabins are now infused with beautiful and durable AM components. Additionally, maintenance spares and repairs are now just a print away, reducing downtime and logistics headaches.
Material Jetting
Material jetting is a 3D printing process that prints objects using a similar method to two dimensional ink jet printers. In this process, liquid material is jetted onto a build platform in layers, and hardened by UV light after each deposition. The print head can deposit different combinations of materials such as polymers and waxes. This allows for printing with a variety of colors and textures. The technology is also capable of mixing hard and soft or opaque and transparent materials. This creates an amazing array of possibilities for creating unique products and prototypes.
Like other 3D printing methods, the first step is to design a product or object using a computer program. This is typically a CAD (computer-aided design) software such as AutoCAD or the free and open-source programs like SketchUp or Blender. The design is then saved as a file in a format recognizable by the 3D printer, usually a.STL file or a.OBJ file. Many commercial and free CAD software programs are available to assist with the creation of designs, or users can find existing designs online.
After the file is created or selected, the printer can start building the object. SLS machines thermally fuse or sinter powdered material layer by layer, while MJF machines use a process called Multi Jet Fusion to fuse the object by fusing the polymer chains within the material rather than binding or glueing them together. This is what makes MJF printers more accurate, functional and durable than SLS machines.
MJF printers can also produce parts with a glossy finish that looks more polished than a traditional print. This is possible because the resins used for supporting structures are optimized to allow them to be easily removed after printing. This is because they can be dissolved with certain chemicals or washed away by water.
Another great advantage of MJF printers is the ability to print in full color. This is a major selling point and has found applications in the medical industry, where models of patient data such as an MRI or CT scan can be printed in color to help doctors and surgeons visualize and plan operations. This can greatly reduce surgery time and improve patient outcomes.